A common objection to doing an energy audit is that ‘Everything is fine’. This is rarely the case.
Here are two examples when audit uncovered saving opportunities that clients did not know existed because they believed everything was in perfect state already. Efficient equipment does not equate to efficient operation.
Sanitation staff turned ‘ON’ fume hoods at night at industrial kitchen
An industrial kitchen had a strict SOP: turn off fume hoods by the end of cooking. Employees followed the procedure: hoods were off by the end of day and they were still off in the morning. This observation was insufficient for auditors. Auditors installed a thermocouple at the exhaust on the roof for a week and found that hoods were operating several hours every night. Came out that sanitation staff routinely turns hood on along with lighting.
Energy wasted during clean up: $15K on natural gas for heating and $3K on electricity for HVAC.
A number of simple low-cost solutions can eliminate this waste: timer, thermocouple-based block, interlocking hoods with ovens.
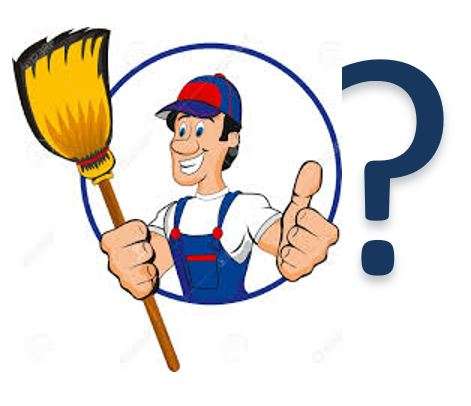
Error in heat exchanger installation made it useless at meat packing plant
Following a professional advice from a prior audit, an advanced meat packing plant redirected reject heat from refrigeration plant to preheat hot water. A $200K heat exchanger was installed and run 24/7.
However, installation was performed without an oversight from prior auditor. Who needs extra costs, right?
Two years later a new audit submetered newly installed heat exchanger and found that electrical cost of pumping exceeded savings on natural gas in water heating. A mistake in installation caused very low delta-T, thus rendering the whole heat exchanger highly inefficient.
Correction of mistake cost less than $2K, but wasted energy could not be recovered.
Energy audit, as annual physical, must be done regularly to ensure money is not wasted.
These examples were suggested by our partners at Enviro-Stewards.
Leave A Comment