Since energy is used by machines, energy use reduction can often reduce a need in new machines, which would have otherwise require CAPEX. “Reduce usage first, upgrade machines second ” is the golden rule of CAPEX-efficient energy management. Order of project implementation can have huge effect on the amount of CAPEX required and complex audit helps establish the most efficient order.
Here are two examples of how it works.
A small change helped avoid refrigeration plant upgrade at cheese maker
Due to continuous growth, an industrial cheese making plant experienced shortage of refrigeration capacity. A $180,000 equipment upgrade was budgeted. A shiny new compressor was on the horizon. Luckily for CAPEX budget an energy audit was conducted before upgrade.
This plant operated a cheese smoker located within a refrigerated room. Production process required opening doors of smokers to load and offload cheese. Since with open doors smoke comes into the room, an exhaust was installed above smoker doors to ensure employee safety.
Using direct metering, audit has found that smoker doors were open 5 min every hour, while exhaust worked non-stop.
For 50 minutes of every hour refrigerated air was unnecessarily exhausted.
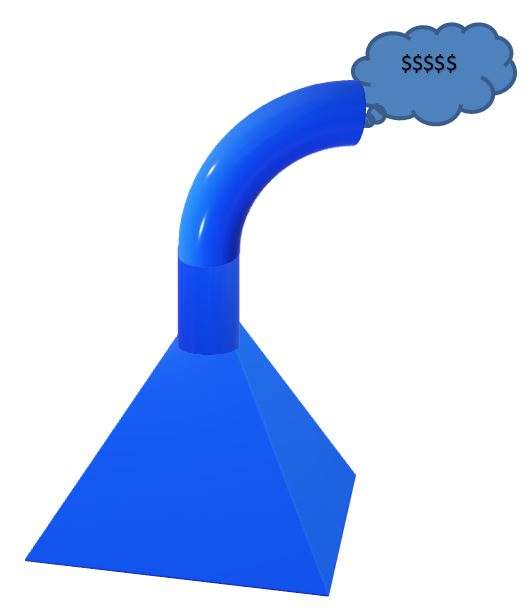
Unnecessary air exhaust literally throws your money up the chimney
Interlocking smoker doors with exhaust fan (with additional timer) allowed to save an estimated $30-40K on electricity on exhaust fans alone. Great result for a $5K upgrade. However, this was icing on the cake of real savings:
- Reduction of air exhaust from refrigerated room reduced cooling load and eliminated need for refrigeration plant upgrade – $180,000 of CAPEX
- An upgraded refrigeration plant would have used an estimated extra $112,000 in electricity to run
Heat exchanger reduced CAPEX from $200K to $75K at a chemical manufacturer
This chemical plant produced liquid product that required heating and cooling. Growth of production volume was limited by undersized boiler and cooling tower that was too small for previously upgraded compressors.
When a facility is short of both heating and cooling an energy efficiency opportunity just waits to be found. Audit suggested using hot gas from refrigeration plant to preheat liquid product through a heat exchanger. With heat transfer from hot gas to product, less heating was required from boiler and less cooling was required from refrigeration plant’s condenser, which, in turn reduced load on cooling tower.
A $75K heat exchanger eliminated a need for a $150K boiler upgrade and for a $50K cooling tower upgrade.
Saving of natural gas and water came as a welcome extra.
These examples were suggested by our partners at Enviro-Stewards.
Leave A Comment