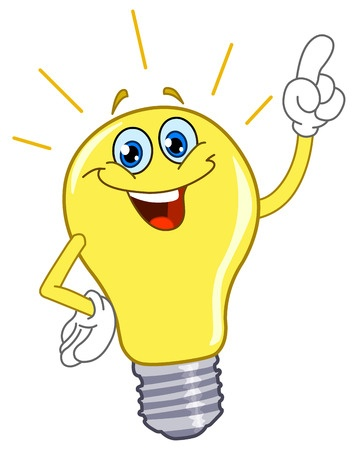
Proper measurement and verification of achieved savings is a key factor when calculating payback period, IRR for an investment into energy efficiency project and any other in-company ratio. Effectively, M&V may mean a difference between energy efficiency project being named a financial winner or a loser, a new funds being allocated to energy efficiency work or not, purchase of new equipment approved or not, incentives granted or not, even annual bonus and promotion … or not; you name it, if it deals with energy efficiency – it depends on M&V.
Measurement and Verification of energy savings is a difficult process. Mainly because business operational conditions change all the time: occupancy, production level, shipment schedule, operation schedule, SKU, outside temperature, humidity – all these factors may affect energy consumption and therefore – visible results of implemented changes.
There is no one-size-fits-all solution for M&V. To deal with the complicacy international community of energy engineers and energy managers have developed a set of rules and recommendations aimed to practically determine savings – International Performance Measurement and Verification Protocol, IPMVP.
Below I have presented what is probably the shortest and drastically simplified version this protocol you will ever see. The full version is about 100 pages; it is available at www.evoworld.org.
Energy Saving Measurement and Verification
To properly account for energy savings achieved through implementation of an efficiency measure one should:
Before changes are implemented:
- Understand what drives energy consumption. Is it a need for light, for fresh air, for cooling, for baking, for moving? Several drivers may affect consumption.
- Figure out what is the minimal full cycle of this driver(s) – a shift, a day, a week, a production cycle, a season, a year?Record any other operational conditions that are considered constant, but that affect energy consumption, such as number of shifts, number of employees, operation hours and schedule, truck loading procedure.
- Figure out how fast this driver changes through the cycle and how fast these changes affect consumption. If frequent changes do not affect consumption, then less measurements is required.
- Using 2 and 3 determine min number of measurements of both (!) energy use and driver(s). Driver may be measured in degrees, sqft, kg, liters
- Collect data determined in 4 “before” change through a cycle determined in 2.
- Determine the baseline consumption model through regression analysis of data collected in
- Ensure that model is statistically valid.
When “after” comes:
- Verify if conditions established in 2 are still valid; if they have changed – figure out how to modify your baseline energy consumption model
- Collect data exactly like in 5
- Forecast “after” consumption using the baseline consumption model
- The difference between forecast and actual consumption is the achieved energy savings.
Calculation of the financial value of achieved energy savings is a whole new story, which we partly discussed in this post.
[…] I wrote more about implementation steps of Option B in a previous post. […]
[…] 9. Lack of post project accountability: after retrofit is completed, who and how determines sustained effect? Uncertainty about long term results causes C-level to hesitate about new projects. Properly set up Measurement and Verification will prove results, read more in How to measure saved energy. […]