We often hear: “Our plant runs at top energy efficiency because we use these procedures and settings and our efficient equipment is fully operational.” Just how often is this true?
With all due respect to maintenance and operational staff, recommendations of a proper energy audit are based on direct observation of operations and lots of measurements. Routinely results of direct measurement contradict existing beliefs about the state of affairs. This is not an evil intent here: bypasses activated for repairs are forgotten, machines deteriorate, contractors rely on each other, and so on.
Here are several examples of how existing beliefs were proven to be wrong and painfully expensive during audit.
a. Belief: “second compressor of refrigeration plant comes online when the first one can’t meet the cooling demand”.
Fact: second compressor comes online randomly due to wrong settings; uncovered through direct power draw measurement. Estimated energy waste is about 110,000kWh per year.
b. Belief: “all condenser fans work, I have just climbed to the roof to check”.
Fact: inner blades broken on 2 out of 3 fans, loss of 50% of air movement caused compressors to work harder
Audit uncovered that identical fans draw significantly different power. Blades were broken on inner propellers, that are not visible while outer propeller is spinning.
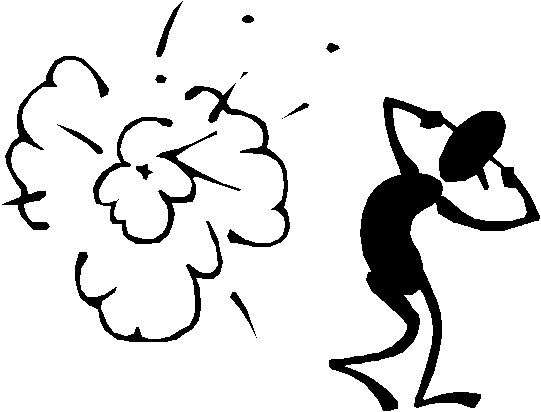
c. Belief: during defrosting evaporator fan stops.
Fact: fan does not stop, it blows hot air into freezer; error in settings causes energy waste AND deteriorated storage conditions
Audit uncovered this by directly measuring power draw on fans.
d. Belief: we barely add water through this pipe, water consumption is negligible.
Fact: pipe is used 16h a day, causing waste of water and chemicals. Estimated cost is $20,000 per year.
e. Belief: temperature in this pot is maintained within a narrow range, if it exceeds range – alarm will sound and red light flash.
Fact: temperature is up by 25F, alarm wire was torn off by some disgruntled worker. Minor failure of controls triggered alarm and disgruntled worker did not like the sound. Overheating caused waste of natural gas for heating and carbon dioxide for cooling down the production process at a total estimated cost of $22,000.
These efficiency opportunities were uncovered during audit through observation and measurement. All of them were believed to be non-existent by maintenance staff.
Direct metering is a key to hidden treasures of energy savingsĀ
Leave A Comment